



0097126282401
00971502045610
CABLES
Instrumentation and Control Cables 300V, 500V, 600V
Single & Multi-pair, PVC, PE, XLPE, LSZH insulation. Individual & collective screen, armour. PVC or LSZH Outer sheath, Fire resistant types acc. to IEC & BS
Standard: EN50288-7 / BS / NEK / IEEE

Thermocouple Cables (ANSI & IEC Code)
Single & Multi-pair , Conductor with solid or stranded alloy PVC, PE, XLPE, LSZH insulation. Individual & collective screen, armour. PVC or LSZH Outer sheath.
Standard: EN50288-7 and ANSI MC 96.1 or IEC 60584-3 for callibration

Fieldbus Cables
Industrial Ethernet, Profibus, Foundation Fieldbus, Device Net,
Mod Bus RS232 / RS485, Profinet
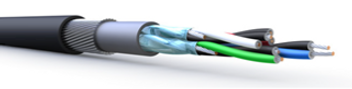
Medium Voltage Cables up to 45kV
1 & 3 conductores, XLPE – EPR – HEPR insulation, armour, PVC, PE or LSZH Outer sheath
Standard: IEC60502-2

Low Voltage Power Cables up to 3kV
Single & Multi-conductor , PVC, PE, XLPE, LSZH insulation armour. PVC or LSZH Outer sheath, Fire resistant types acc. to IEC60331
Standard: IEC60502-1

Special Solutions – Halogenfree cables
In a significant number of cases, physical degradation problems have emerged, such as cracking in the Outer Sheath. These problems are generally produced when the cables are installed at high temperature environments, above 50 ºC. In addition, other factors like the armour in the design and a faulty installation process can also originate the appearance of the problem.

Challenges
The solution to this problem was to develop new compounds with greater tear resistance at high temperatures in armored cables. All precautions and good practice in the installation process are always recommended but also the cables should provide a better performance to prevent the cracking appearance. Thus, the outer sheath compound should guarantee a tear strength value above 5 N/mm, in a range of temperatures exceeding 50ºC. This new developed compound was the challenge for our COCC (Center Of Competence Compounds).
The solution found was highly useful. The appearance of cracks in the outer sheath forces the replacement of cables with the associated maintenance costs that this entails, both in product and time and other costs, production stops, etc. The SUMSAVE® compound avoids this kind of cost.
Value

Special Solutions – S-Block Multilayer-Sheath
In applications where cables may be subjected to attack from concentrated aromatic hydrocarbon, solvents or other chemicals, the standard outer sheath materials are not enough protection for the cable. Then, an extra protection (barrier) layer is needed.

Solutions
There are 2 solutions for this purpose:
Lead sheath. Traditional solution, consisting in a lead extrusion over a PVC bedding.
S-Block. chemical protection, consisting in a 3 layer combination, which provides similar chemical protection to lead sheath, but offering significant advantages 1.Conductor
2.PVC, PE or XLPE Insulation
3.Individual pair screen (optional)
4.Wrapping polyester tape
5.Tinned copper drain wire
6.Copolymer/Aluminium tape, impermeable to moisture and protection against EMI.
7.High density polyethylene (HDPE) bedding, resistant to inorganic chemicals
8.Extruded polyamide 12 layer (Nylon), resistant to organic chemicals and termites
9.Steel wire armour (SWA)
10.PE, PVC or LSOH outer sheath.
S-Block AP protection layer offers, in comparison to traditional lead sheath:
Cable weight is reduced up to 70%
Overall diameter is reduced up to 20%
Bending radius is reduced up to 25%
Termination time is reduced up to 50%
Environmentally friendly
Less hazardous to health
Cost is up to 20% lower

WHY SUMCAB?
Value proposition for our customers High quality standards
Short response times – Quick decision making
Reasonable MOQ from 100 meters productions
Short delivery times, from 2 weeks production time
Best commercial conditions & service
Guarantees of a large company, flexibility of a small business
Deep understanding of End Users needs
Cable knowledge – COC dedicated exclusively to OGP Projects
Logistics centres in major national sea ports: Barcelona, Bilbao, Valencia
Complete portfolio range for industrial plants
